Resources
Explore our blogs, guides, videos, customer case studies and more to learn how Anark can help you innovate faster.
Filters
Events
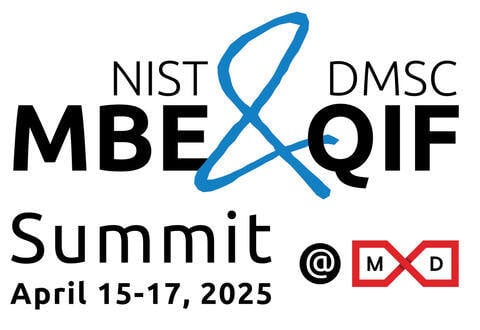
Events
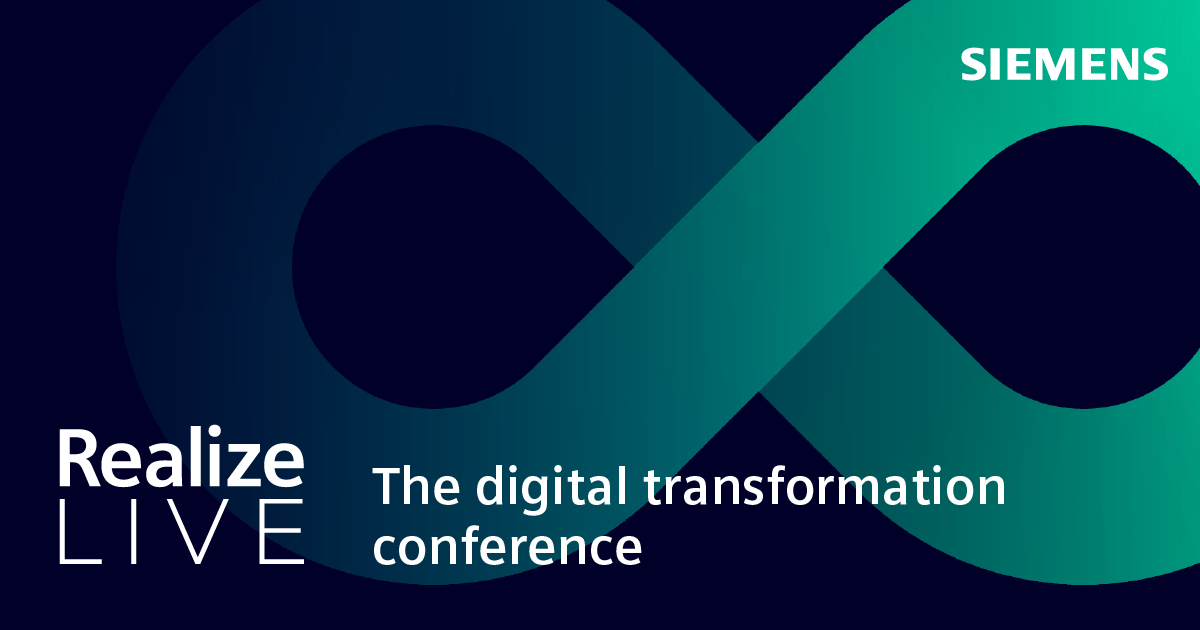
Events
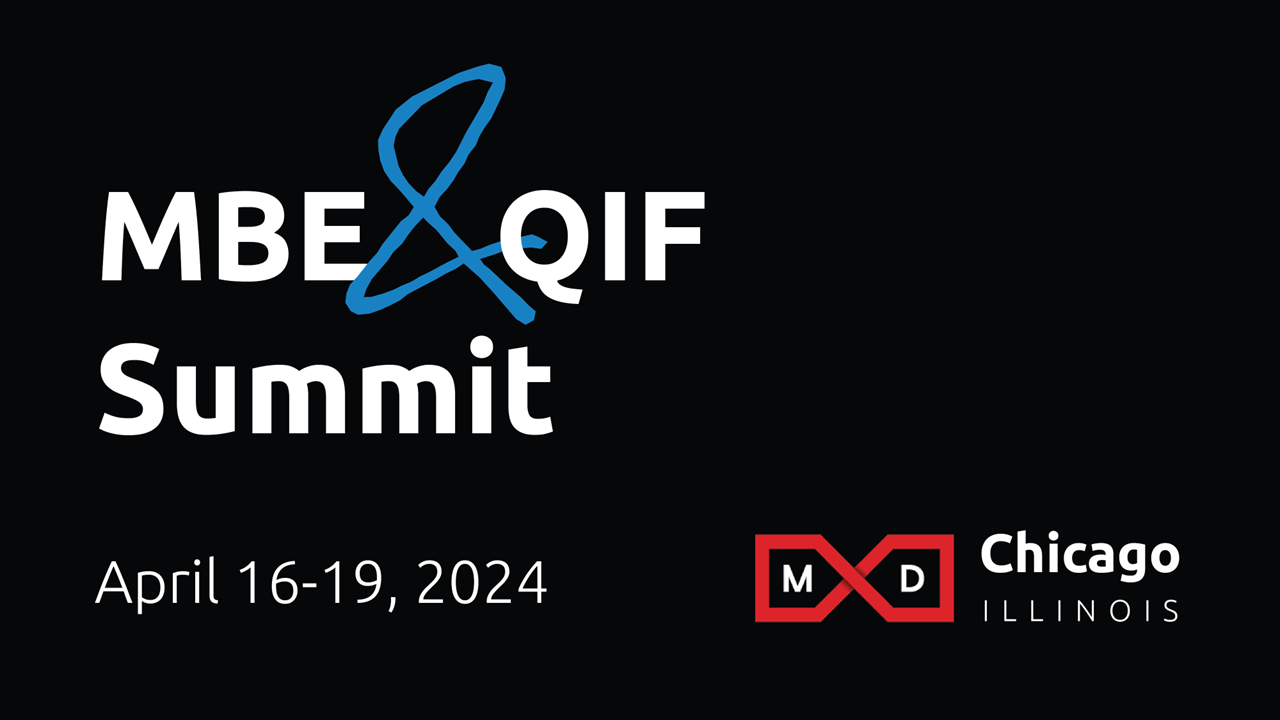
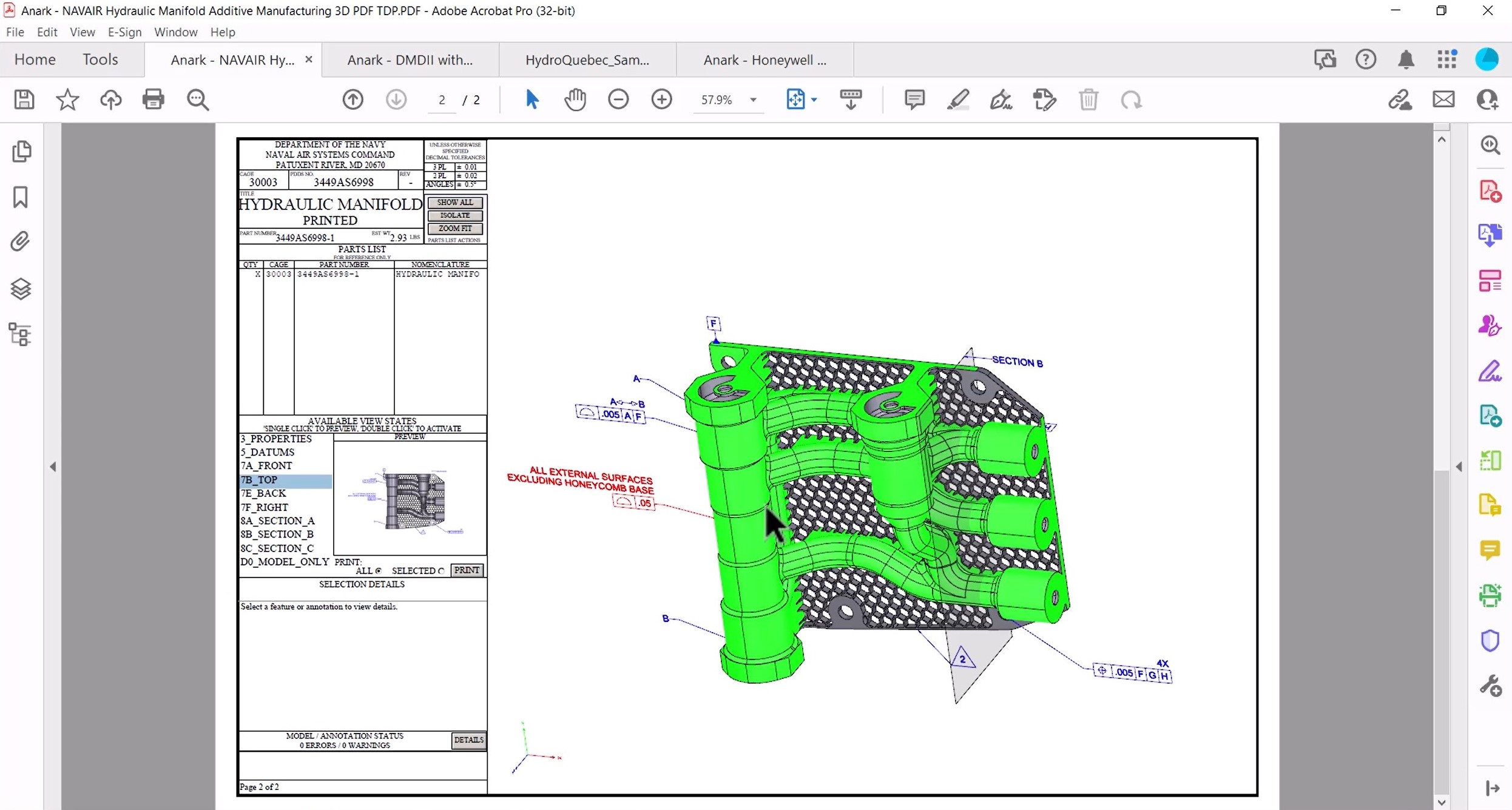
Videos
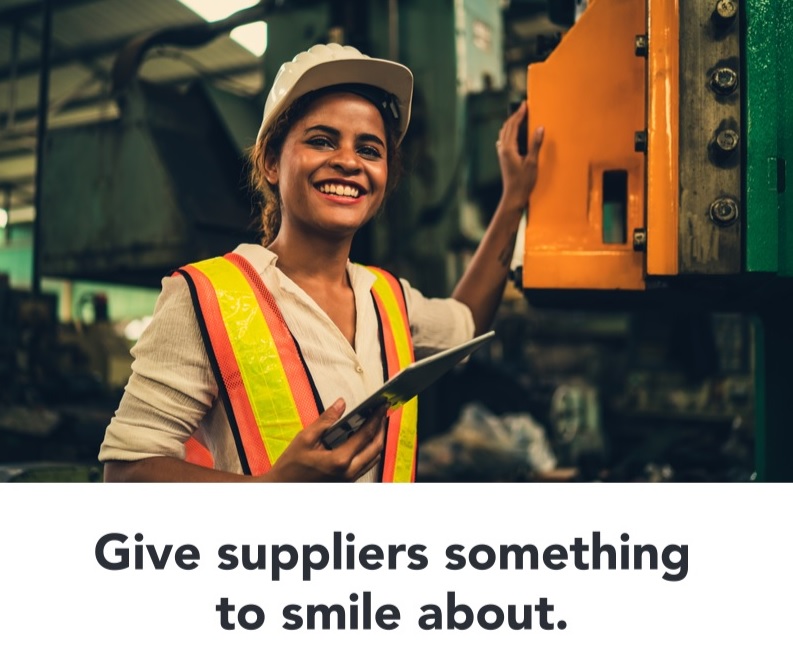
Data Sheets
Events
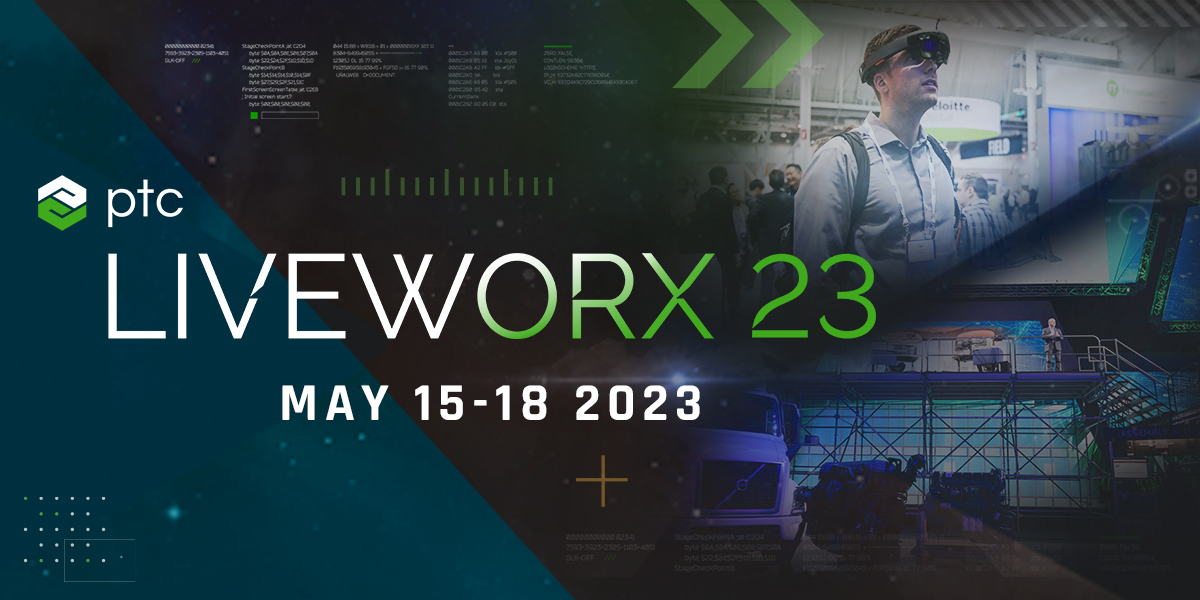
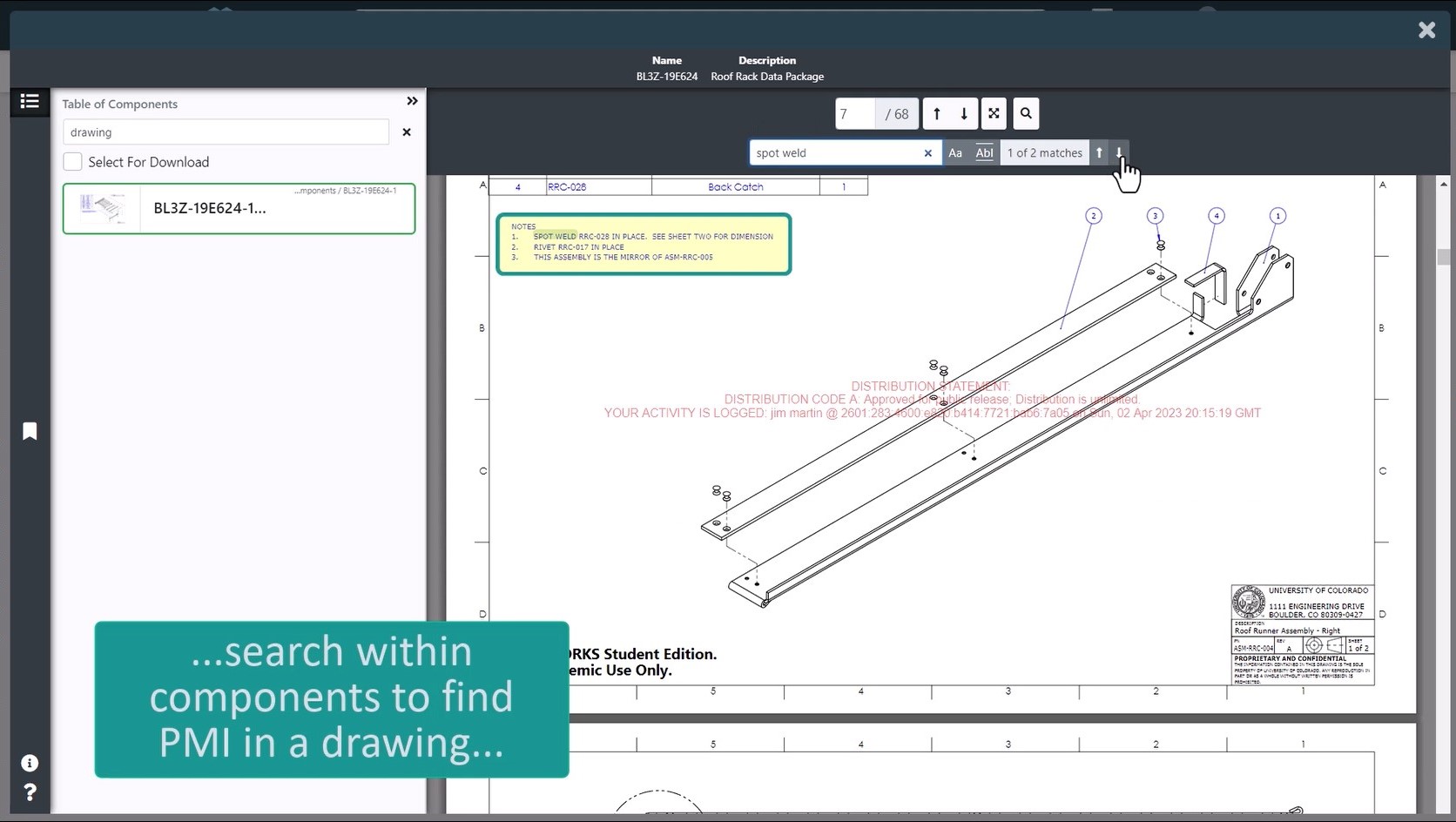
Videos
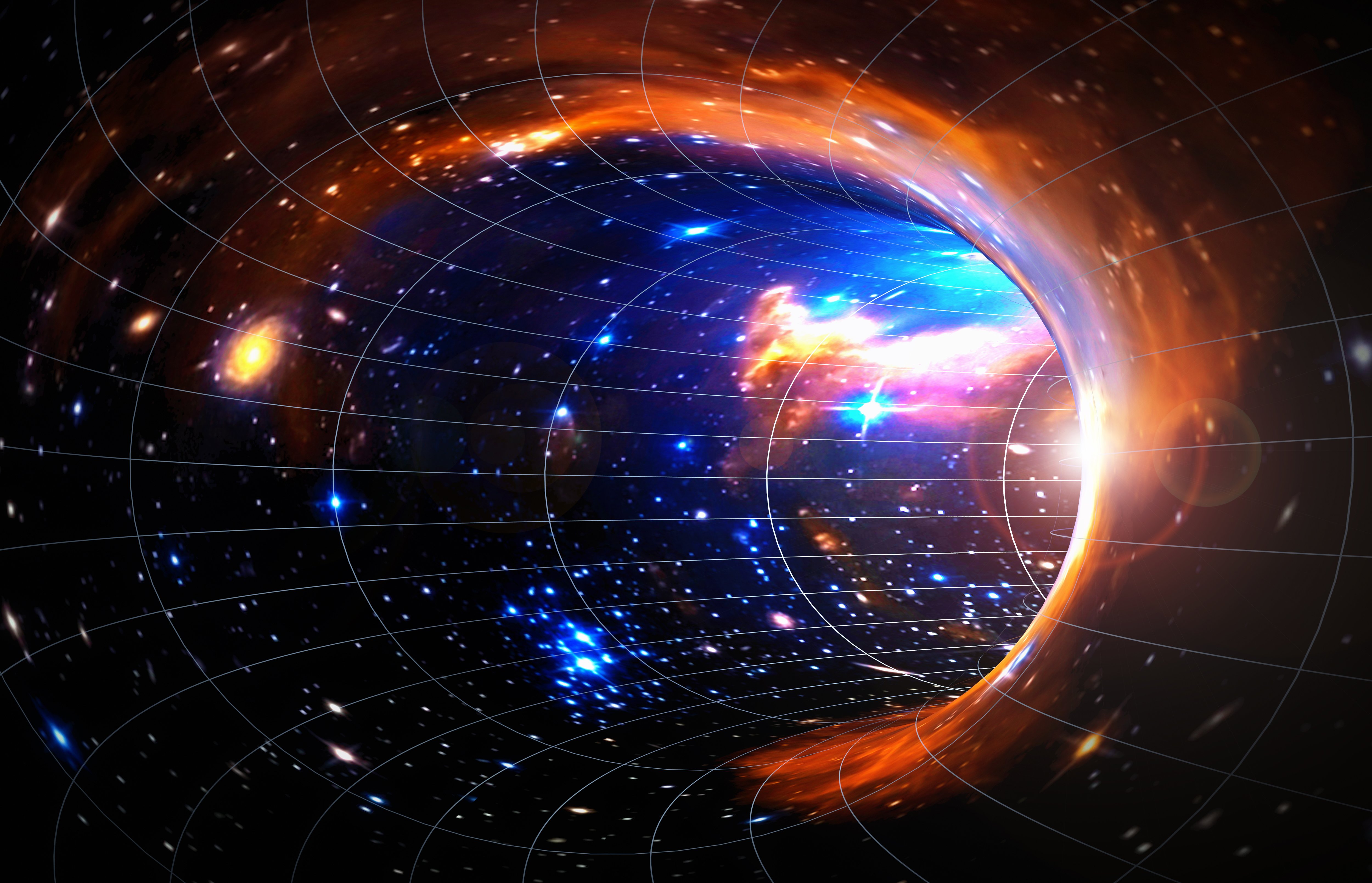
Data Sheets
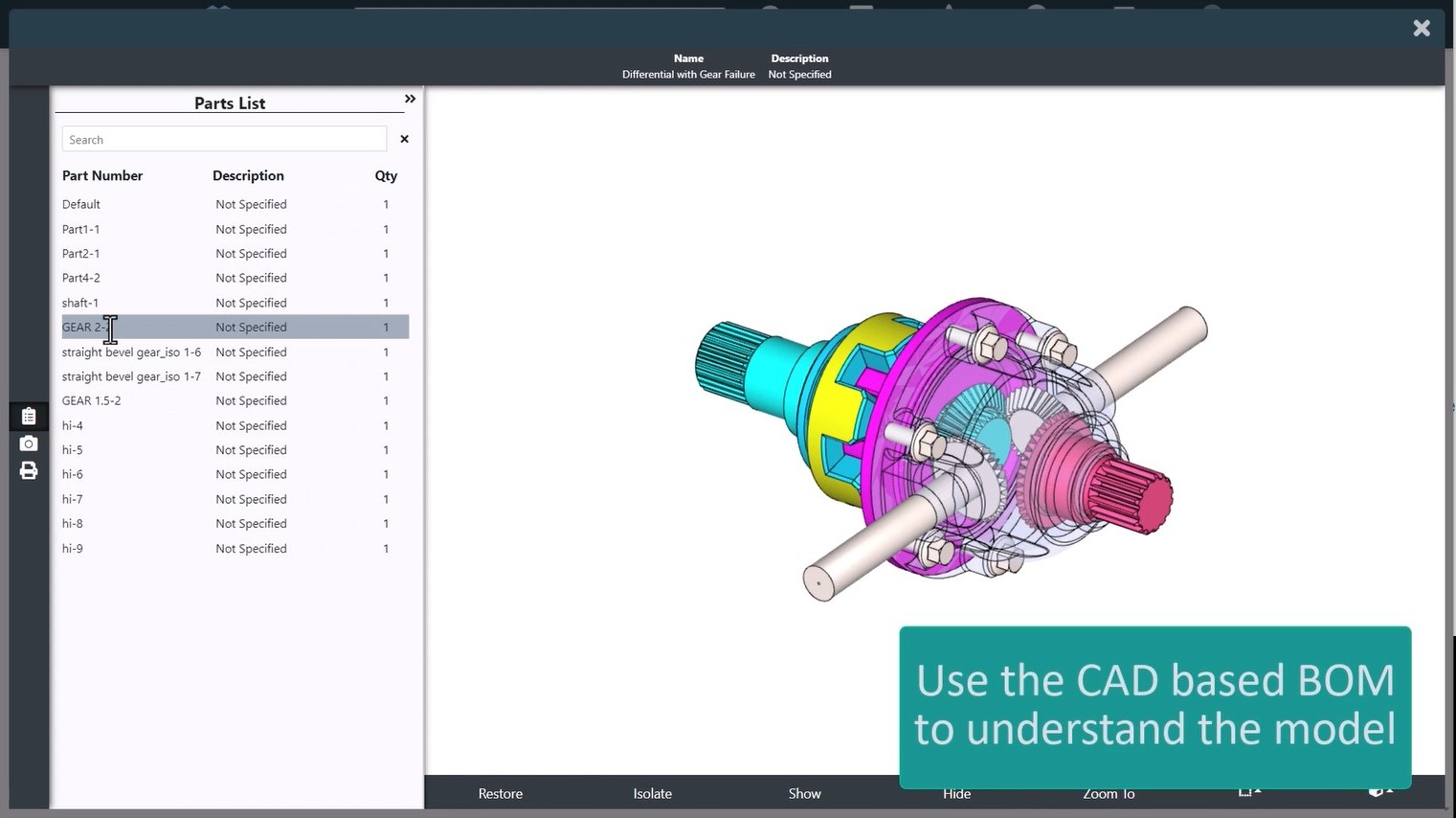
Videos
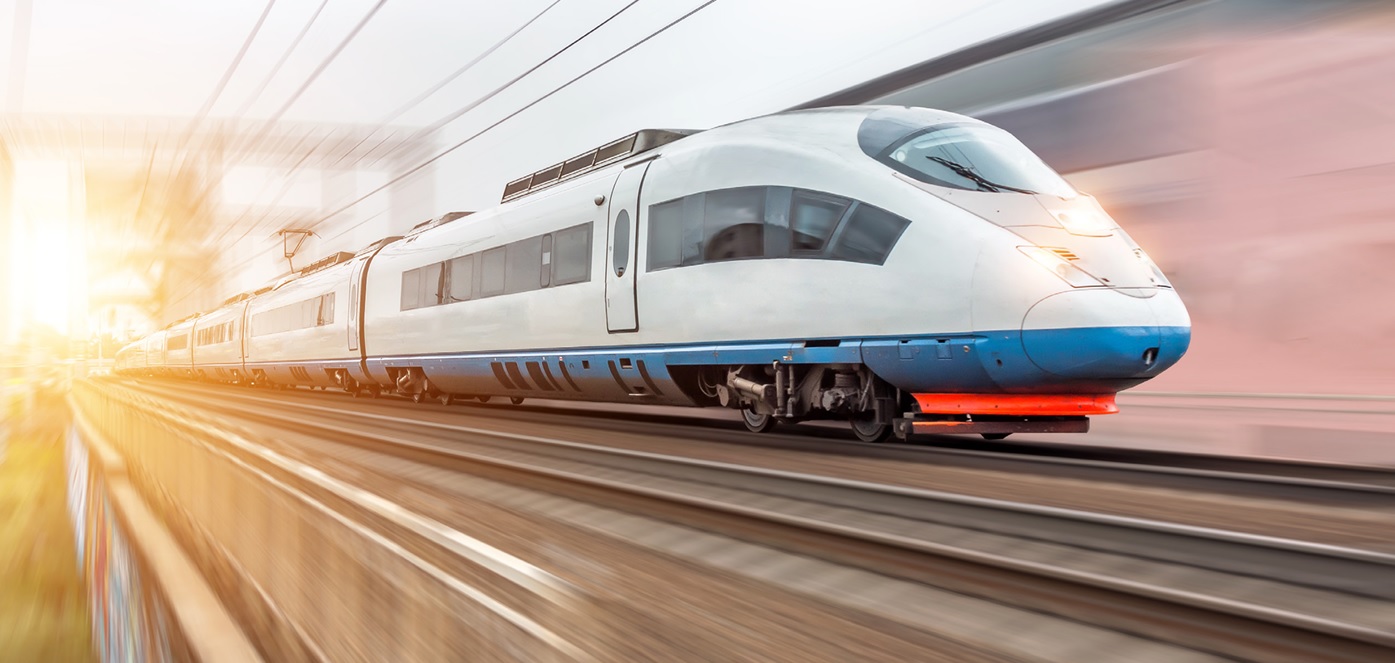
Data Sheets
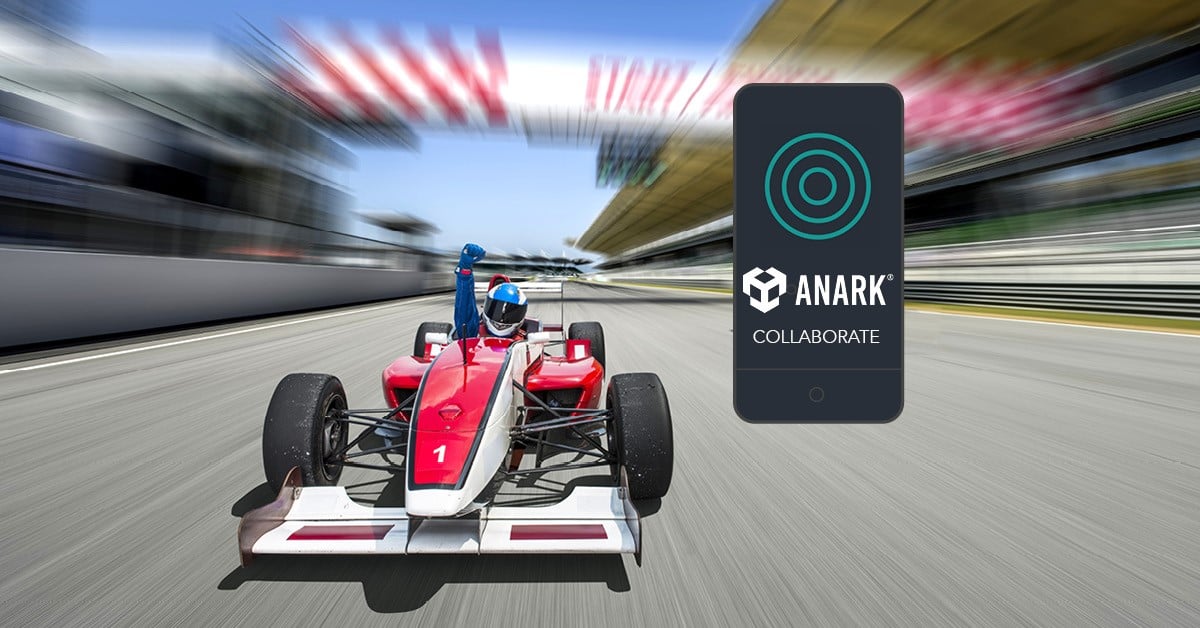
Data Sheets
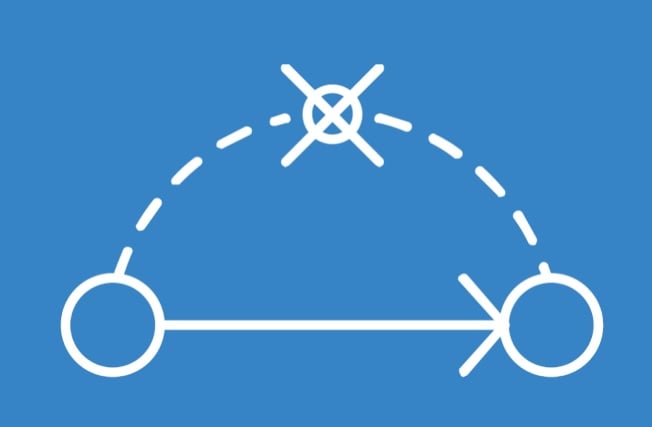
Guides
Events
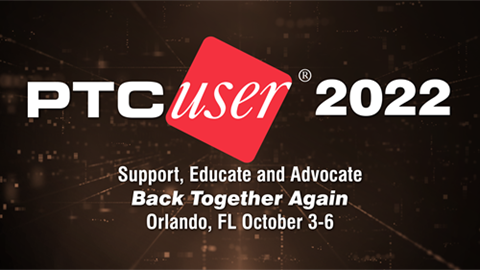
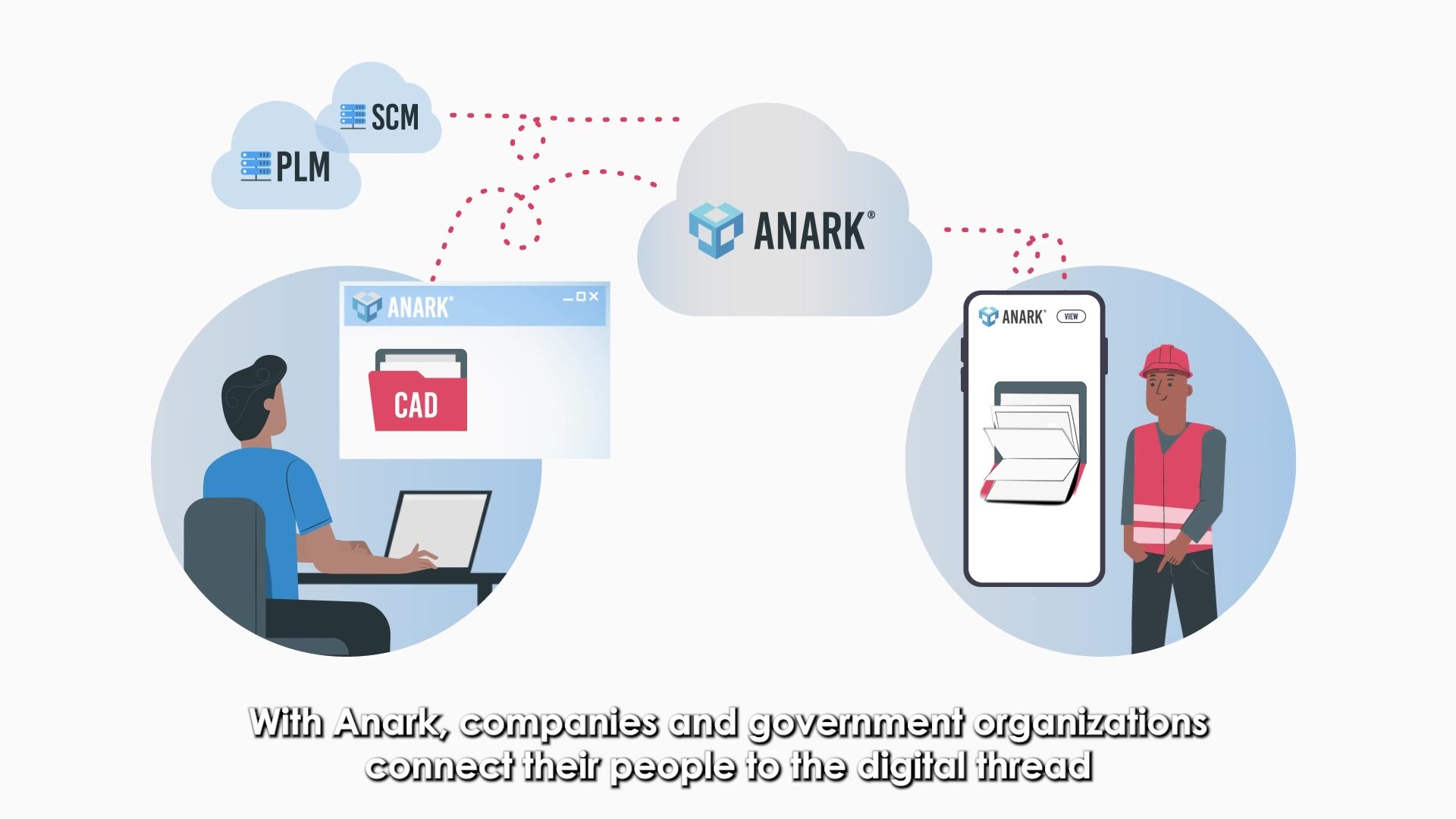
Videos
Events
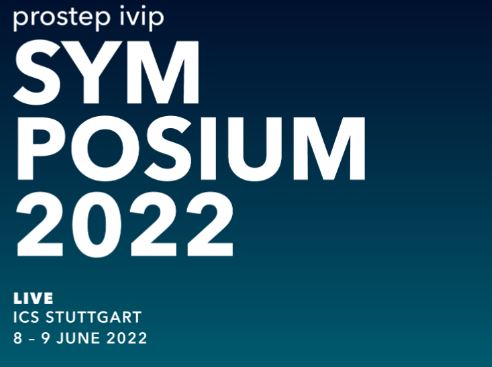
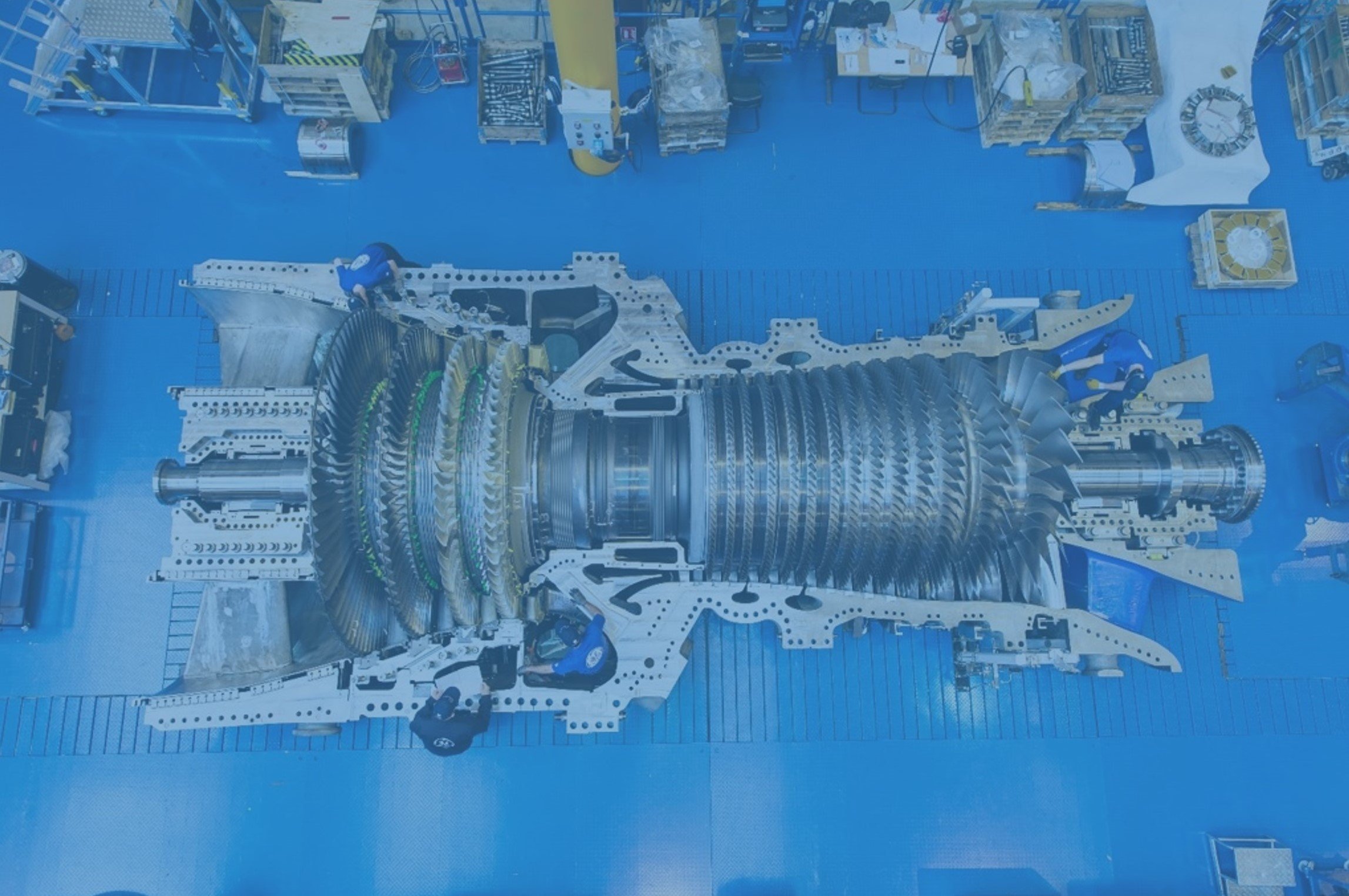
Case Studies
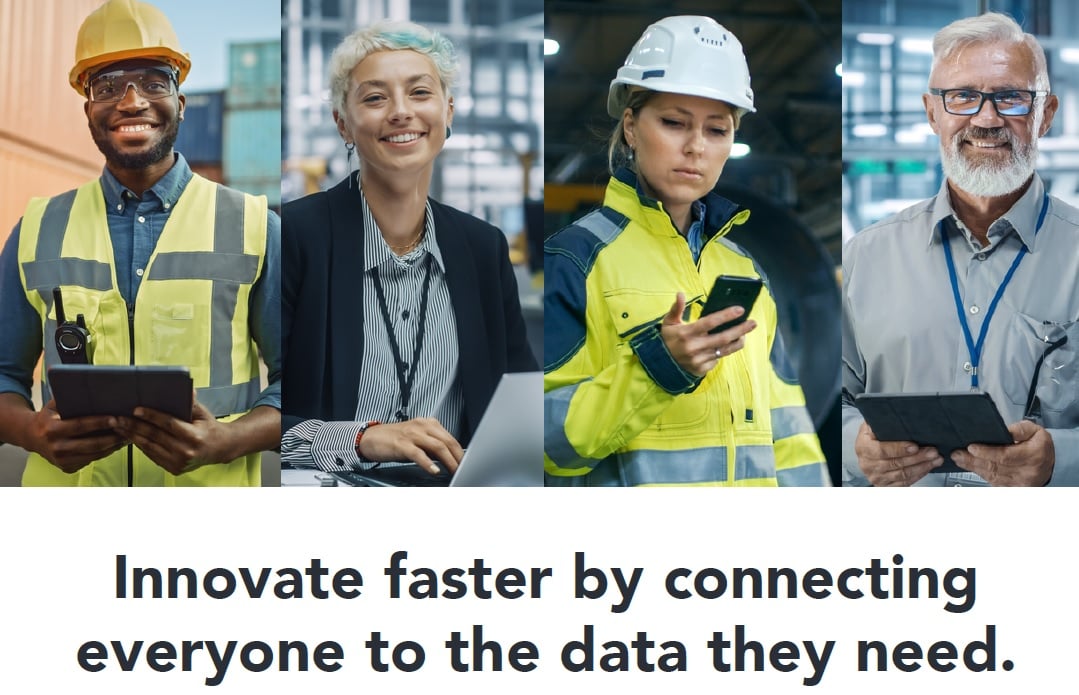
Data Sheets
✕
✕
Watch the Overcoming the Digital Thread Myth with Modern Collaboration - 3D CIC Replay Video Now!
✕
Watch the Anark 3D PDF Overview Video Now!
✕
Watch This Webinar On-Demand
✕
Watch the Video: Deliver MIL-STD-31000B Compliant 3Di PDFs to the DoD Video Now!
✕
Watch the Anark Publish automation with Windchill Packages Video Now!
✕
Watch the 3D Model Based Information in One Click Video Now!
✕
Watch the Anark Workstation R74 Highlights for Work Instruction Authoring Video Now!
✕
Watch the Fast, Flexible, Smart Search Video Now!
✕
Watch the Configurable Smart Watermarks for Enhanced IP Security Video Now!
✕
Watch the Product Data Sharing and Collaboration Quick Start Video Now!
✕
Watch the Visualize Solidworks Designs Video Now!
✕
Watch the Content Items Contain the Product Data You Need Video Now!
✕
Watch the Drag Drop and Collaborate on Solidworks Designs Video Now!
✕
Watch the Anark - PTC Windchill Integration Demo Video Now!
✕
Watch the Anark - PTC Windchill Integration Overview Video Now!
✕
Watch the Anark Overview Video Now!
✕
Watch the GE Power’s Transformation and Solution Video Now!
✕
Watch the Technical Content Collaboration Video Now!
✕
Watch the Anark Collaborate Mobile First User Experience Video Now!
✕
Watch the Transforming GE Power’s Digital Supply Chain Video Now!
✕
Watch the Securely Manage Supply Chain Communication with Anark Collaborate Video Now!
Ready to connect your team?
Discover how we connect teams to the technical data and expertise they need.