By Patrick Dunfey
If you have ever tried to do something yourself (change your car’s oil, home repairs/renovations, tuning your bike, sell your house, sizing a new market for product launch) you know how helpful expertise is in addition to the information you have. You also understand the cost of mistakes: project delays, opportunity cost, and the cost of fixing mistakes. I regret to say that I’ve personally lost a week of time, and significant cost trying to change out a bathroom sink. If someone had looked at it with me before getting started, I would have avoided a fit problem with the new sink that left the project half-completed for a week while I purchased 3 different adapters to eventually solve the problem. I wished there was a better way.
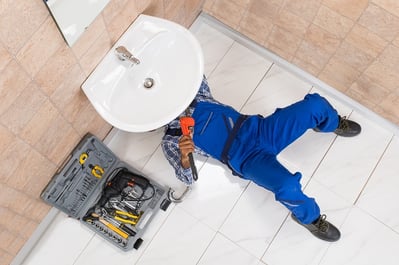
The good news is that this is readily available for the vast majority of work that is done every day in the digital cloud-based era we are in. In fact, you can do this very thing with documents and presentations where multiple people simultaneously review and comment in the document while talking about the work they are doing. This is changing the way people work with one another in tools like Microsoft Teams.

The leaders in manufacturing are finally breaking free of communication tools like email and chat that limit the performance of their product development teams. And the advantages these companies stand to gain are significant as they move from technical data sharing to technical data collaboration portals that connect people to more than just the information and data they need. It connects them to their teammates, specialists, experts, suppliers and even their customers. Contextual collaboration at it’s finest.
If only I had that for my bathroom sink.